HPMC for Cement Render
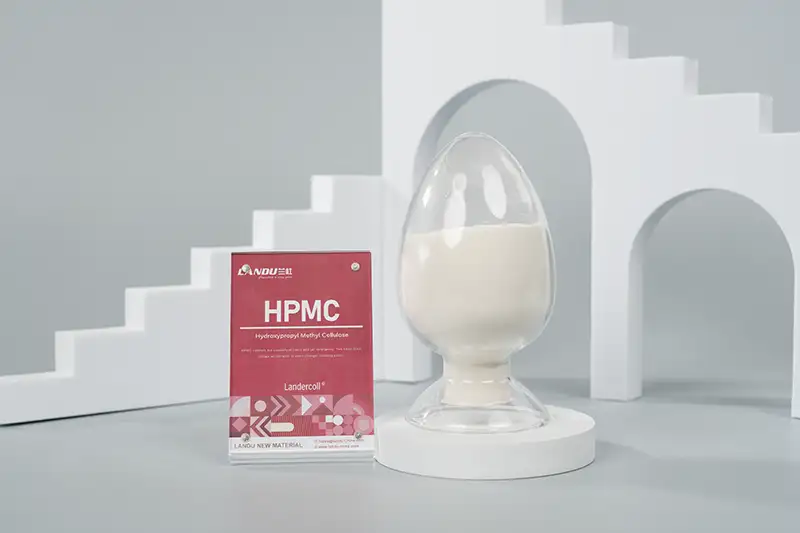
HPMC for Cement Render
Key Takeaways
- HPMC is a versatile cellulose-based additive that enhances the performance of cement-based materials.
- HPMC improves water retention, workability, and adhesion properties of cement renders, leading to enhanced construction quality.
- Understanding the chemical structure and manufacturing process of HPMC provides insights into its functionality in cement rendering applications.
- Proper application techniques and mixing ratios are crucial for maximizing the benefits of HPMC in cement renders.
- HPMC-modified cement renders exhibit superior strength, crack resistance, and long-term durability, making them an essential choice for modern construction projects.
Understanding HPMC and Its Role in Construction
HPMC, or Hydroxypropyl Methylcellulose, is a key chemical in modern construction. It’s made from cellulose and has special properties. These make it great for improving cement products, boosting their quality and performance.
Chemical Structure and Properties
HPMC is a modified cellulose with glucose units and hydroxypropyl and methyl groups. This mix gives it great water retention and workability. It also improves adhesion, making it essential for cement products like mortars and plasters.
Basic Functions in Construction Applications
- It keeps water in cement mixtures, stopping them from drying too fast and making them easier to work with.
- It helps cement stick better to surfaces, creating a stronger bond.
- It makes the mixture easier to spread, ensuring a smooth finish.
- It helps create a uniform texture in the final product.
Benefits of HPMC for Cement Render
Benefit | Explanation |
---|---|
Improved Workability | HPMC’s thickening and water-retaining properties create a smoother, more homogeneous cement mixture, making it easier to apply and spread. |
Enhanced Durability | HPMC improves the cement’s adhesion to the substrate and reduces shrinkage and cracking, resulting in a more resilient and long-lasting render. |
Increased Strength | HPMC enhances the overall cohesion and binding properties of the cement mixture, leading to stronger and more durable final products. |
Improved Crack Resistance | HPMC’s ability to reduce shrinkage and cracking helps to prevent the formation of cracks in the cement render, improving its long-term performance. |
Using HPMC for render makes the cement mixture easier to work with. Its thickening and water-retaining properties create a smooth consistency. This makes the render simpler to apply and ensures a uniform, attractive finish.
HPMC cement render also lasts longer and is more resistant to cracks. It helps the cement stick better to the surface and reduces shrinkage and cracking. This means the render is more durable and needs less maintenance, lasting longer.
Moreover, HPMC as a construction additive boosts the strength development of the cement render. It improves how well the mixture sticks together, leading to a stronger, more durable final product. This ensures the render can handle the demands placed on it.
In summary, adding HPMC to cement render brings many benefits. It improves workability, durability, and strength, making it a vital construction additive. HPMC’s versatility is key to delivering high-quality, long-lasting cement render solutions.
Key Properties That Make HPMC Essential for Rendering
Water Retention Capabilities
HPMC stops the render from drying too fast. This lets the render stay workable. It makes applying the render smooth and easy.
Workability Enhancement
HPMC also makes cement renders easier to work with. It makes the mixture flow better and be more flexible. This makes applying the render smooth and even.
This also means less effort and more efficiency. It makes the rendering process better.
Adhesion Improvement
Adhesion is key in cement rendering. It’s what holds the render to the surface. HPMC’s special structure makes the render stick better.
This strong bond prevents problems like the render coming off. It keeps the render in place for a long time.
Proper Application Techniques and Mixing Ratios
For HPMC application, mixing well and consistently is the main goal. Add HPMC to the cement mix in the right amounts, usually between 0.1% to 0.5% by weight of cement. The exact mixing ratio depends on the project and what you want the final render to look like.
- Make sure the surface is clean, dry, and free of dirt or other stuff.
- Mix the cement, sand, and HPMC until it’s all the same.
- Spread the HPMC-infused cement in thin, even layers with a trowel or similar tool.
- Let each layer dry a bit before adding the next, following cement render techniques well.
- Keep the new render away from fast drying, direct sunlight, and strong winds to avoid cracks or uneven drying.
HPMC Concentration | Cement Render Characteristics |
---|---|
0.1% by weight of cement | Improved workability and water retention |
0.3% by weight of cement | Enhanced adhesion and crack resistance |
0.5% by weight of cement | Increased strength and long-term durability |
“Proper HPMC application and mixing ratios are essential for achieving the desired performance and aesthetics in cement render projects.”
Impact on Render Quality and Durability
Strength Development
HPMC keeps the right amount of moisture in the render. This helps the render dry and harden well. As a result, the render becomes stronger and more solid.
Crack Resistance Features
HPMC helps prevent cracks in the render. It acts as a glue, sticking the render to the surface better. This makes the render more flexible and less likely to crack.
Long-term Performance Benefits
Using HPMC in render makes it last longer and perform better. It keeps the render moist, preventing it from drying out too fast. This stops cracks and keeps the surface looking good for a long time.